Pompes et moteurs : des progrès en compacité et en efficacité
La fiabilité et le rendement constituent les points d’entrée du marché des moteurs et des pompes mais les utilisateurs sont de plus en plus nombreux à demander des versions compactes de même efficacité. Avec l’électrification, les fournisseurs développent par ailleurs des solutions réduisant le niveau sonore des composants hydrauliques dont le bruit n’est plus couvert par celui du moteur diesel.
Fiabilité, rendement, compacité, réduction du niveau sonore, intelligence embarquée : les tendances du marché des pompes et des moteurs mêlent les fondamentaux historiques et de nouveaux engagements des constructeurs. Après l’électrification des moteurs, il faut en effet passer à la refonte des systèmes hydrauliques eux-mêmes, en travaillant sur leur intégration, le bruit, le rendement global ainsi que le refroidissement, la durée de vie de l’ensemble ou bien encore la lubrification de l’accouplement.
Bosch Rexroth dispose par exemple d’une gamme très étendue de pompes et de moteurs, en termes de cylindrée (de 5 à 1000 cm3/tr) ou de pression (280 bars, 350 bars pour le circuit ouvert, et jusqu’à 500 bars pour le circuit fermé). « Ces produits ont tous été conçus pour des applications à entraînement diesel avec, au cours des années, la focalisation sur le rapport poids/puissance/coût. Avec l’électrification des machines, d’autres critères émergent, qui nécessitent soit l’adaptation des produits actuels, soit l’étude de nouveaux produits. Ces nouveaux critères sont le niveau sonore (ou plus exactement de pulsation de pression), car les moteurs électriques sont beaucoup plus silencieux que les diesels qui cachaient le bruit de l’hydraulique, mais aussi le rendement. Les engins mobiles sont, comme les automobiles, alimentés par batterie, et toute perte évitée devient essentielle pour l’autonomie des engins » résume Philippe Durand, responsable applications/produits pour l’hydraulique mobile.
L’écoconception est également mise en avant. KEB, fabricant de solutions d’entraînement pour la logistique, le médical et les machines-outils notamment, travaille sur la compacité : « Les gammes DM et DA regroupent les moteurs asynchrones conformes à la réglementation d’écoconception UE 2019/1781. Nous couvrons une plage de puissances de 0,12 à 45 kW, classe IE2 jusqu’à 0,55 kW et IE3 à partir de 0,75 kW. Les gammes TA, Dynamic Line 4 et Dynamic Line 3 rassemblent les servomoteurs synchrones à aimants permanents. La plage de couple est de 0,5 à 520 Nm et les vitesses de rotation montent jusqu’à 6000 tr/min » détaille Jean-Yves Geneste, directeur général. KEB assure le complément avec ses motoréducteurs : « Ils disposent d’un montage en direct du moteur sur le réducteur pour une compacité et un poids optimisé. Le programme de servomoteurs s’est étoffé, ces dernières années, avec la nouvelle gamme Dynamic Line 4 et sa plage de couple jusqu’à 520 Nm. KEB dispose également d’une gamme de moteurs asynchrones carrés à vitesse variable avec contrôle vectoriel de flux, jusqu’à 55 kW. Une alternative idéale aux moteurs triphasés classiques offrant une grande compacité et des inerties plus faibles » estime le dirigeant.
Toujours plus d’efficacité
« L’efficacité reste naturellement une voie majeure aussi pour les pompes » explique Alexandre Moalic, responsable des ventes mobiles Parker en France. Outre ses moteurs, dont la nouvelle gamme NX8xHM pour les pompes électrohydrauliques basse tension des véhicules routiers et tout-terrain lancée en octobre 2023, Parker Hannifin propose la majeure partie des technologies de pompes : à piston (cylindrée fixe et variable) pour les plus fortes pressions et les vitesses les plus importantes, à palette (une technologie moins bruyante) et à engrenages. « Nous dépassons les 95 % en termes d’efficacité sur les technologies à piston » souligne Alexandre Moalic.
KEB et Brusatori : des solutions complètes
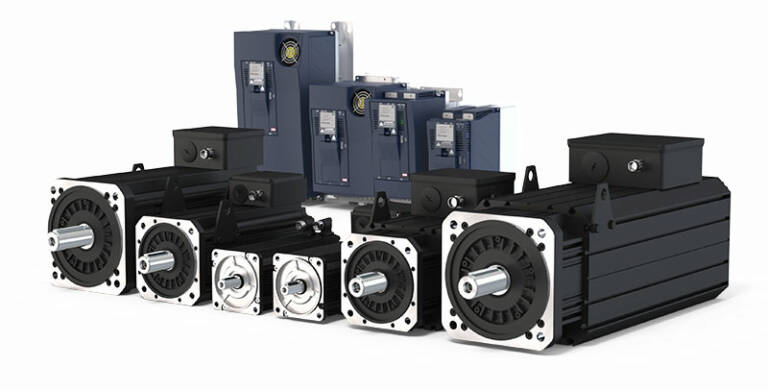
Le marché souligne cette tendance à l’intégration de systèmes moteurs-variateurs. KEB Automation a ainsi repris en 2022 le fabricant italien Brusatori Electric Motors, basé à Milan et qui produit des moteurs électriques depuis 1953. La firme est connue notamment pour ses servomoteurs compacts DL4 à couples élevés (de 5 Nm à 530 Nm). D’abord centrée sur les moteurs asynchrones, elle a vite développé les DC et les moteurs à aimant permanent. Après une collaboration de trois ans, la famille fondatrice a cédé la majorité des parts à KEB. De quoi renforcer l’offre de « solutions complètes » de ce dernier.
L’innovation la plus récente porte sur les pompes à palettes. Elles pourraient dépasser les 4 000 tr/min. « Pour optimiser le rendement et obtenir le meilleur couple, les pompes doivent aller plus haut en vitesse » rappelle-t-il. L’un des intérêts de l’électrification est en effet d’obtenir la puissance à la demande : l’utilisateur veut passer d’un débit très faible au débit maximum très rapidement, ce que permet le variateur de vitesse. Il faut ensuite que la pompe soit capable d’exploiter cet avantage de vitesse variable. « Depuis plusieurs années nous proposons la mise en place de notre solution d’optimisation énergétique ‘‘Power On Demand’’ sur des installations neuves ou existantes pour une production moins énergivore » illustre Patrice Baratte, responsable des ventes d’Oilgear en France.
L’entreprise a élargi sa gamme avec la nouvelle pompe XD5 supportant des vitesses de rotation jusqu’à 2 450 tr/min, voire davantage, pour un faible encombrement. « Cette pompe à cylindrée variable et au temps de réponse rapide répond aux utilisations standards en huile minérale ou avec des fluides à basse viscosité » complète-t-il.
Bosch Rexroth électrifie ses pompes avec une nouvelle régulation appelée EOC (pour Electronic Open Circuit). Le principe consiste à simplifier la pompe en supprimant les différentes régulations hydrauliques pour les remplacer par une commande simple de cylindrée, des capteurs de pression et de cylindrée, puis de déplacer l’intelligence de régulation dans un contrôleur et un software adapté. Ces deux facteurs contribuent à améliorer le rendement, la réactivité mais aussi la contrôlabilité de la pompe et, donc, de la machine. Chez Hydac, qui fournit pompes et moteurs pour les marchés industriel et mobile, les commandes électriques des pompes assurent l’ajustement rapide, facile et précis du débit volumétrique fourni, pour répondre à la demande spécifique de débit des actionneurs dans le système hydraulique. « Notre nouvelle pompe mobile PPV100M, entièrement équipée de capteurs électroniques, est utilisée dans des systèmes de manutention mobiles ou dans des applications forestières » pointe Nicolas Vieillard, chef de projets. Le rendement de cette nouvelle pompe à pistons axiaux (315 bars en pression nominale et 350 bars maximum) va jusqu’à 97 %. Son faible poids contribue aux économies d’énergie des engins mobiles. « Nous venons de compléter notre offre en lançant notre nouvelle gamme de pompes à engrenage denture hélicoïdale PGE300. Elle est maintenant disponible avec des cylindrées allant de 1,6 à 60 cc/tr et se caractérise par de bas niveaux sonores et de faibles pulsations » poursuit le spécialiste.
« Silence, on tourne ! »
« Le niveau maximum de bruit est généré au niveau de la compression. Nous allons pouvoir probablement encore gagner en vitesse pour les pompes, mais nous atteindrons forcément des limites physiques sachant en plus que le bruit augmente quand la vitesse augmente » indique Alexandre Moati. La nouvelle pompe A10VO série 60 de Bosch Rexroth est conçue pour couvrir les applications avec des pressions nominales jusqu’à 280 bars (pression maximale de 320 bars). Elle réduit les pulsations de pression de 50 % pour diminuer les émissions sonores grâce au nouveau système PCV (Pre Compression Volume). « Il s’agit de la première pompe variable à pistons axiaux de Bosch Rexroth pouvant être équipée de ce système en standard. Cette amélioration permet de se passer des mesures classiques coûteuses telles que l’encapsulage du compartiment moteur, le système d’amortissement hydraulique ou l’isolation de la cabine » indique Philippe Durand. Il poursuit : « la densité de puissance de cette pompe a augmenté de 49 % pour une pression jusqu’à 280 bars tout en réduisant sa longueur de 10 % ». La compacité a définitivement sa place dans les cahiers des charges. « L’encombrement sur la machine constitue un aspect important » confirment Clément Lemoine (gérant) et Benoît Picard (directeur technique) d’Inaltis. L’entreprise vend des pompes et des moteurs à engrenages à corps aluminium et, depuis peu, à corps fonte, de la marque Galtech ainsi que des moteurs orbitaux de marque Hydromot. « Les dernières technologies ‘‘tout-en-un’’ combinant pompe ou moteur à piston à débit variable avec distribution intégré pour optimiser la consommation énergie et les mouvements progressent d’année en année, mais restent fragiles et onéreuses. Par conséquent, il faudra toujours des technologies à engrenages ou orbital pour des systèmes simples et avec un coût réduit » estiment les dirigeants. Patrice Baratte, d’Oilgear, rappelle que leur gamme de pompes à pistons autorégulatrice est utilisée depuis longtemps dans les applications sévères travaillant 7J/7 24h/24 (forge, extrusion, bancs d’essais, aéronautique, énergie, défense et marine). « La technologie des pompes Oilgear avec paliers hydrodynamiques permet un fonctionnement avec une grande variété de fluides, notamment les fluides difficilement inflammables, qui intéressent souvent nos clients soucieux du risque d’incendie. Notre gamme brevetée de pompes spécifiques Transfer Barrier® apporte au marché une solution de débit variable industriel pour les applications encore plus particulières (fluides très agressifs, températures de fonctionnement de – 40° à +120°C ou eau pure haute pression) » complète Patrice Baratte.
n matière d’électrification, les applications mobiles sont les premières à évoluer avec, en tête, les minipelles, mais les applications fixes suivent avec, en ligne de mire, les économies d’énergie. « De plus en plus souvent, le couple variateur-moteur est mis en place pour optimiser les process et surtout réduire les coûts énergétiques dans le cadre de la transition agroécologique » confirme Jean-Yves Genest.
Réduire la consommation d’énergie
Les moteurs à haute efficacité énergétique tels que Dyneo+ ont été récemment mis sur le marché par Nidec Leroy-Somer pour les solutions de pompage VIL (Vertical In Line). « De 11 à 500 kW, cette gamme de moteurs synchrones à réluctance assistée d’aimants sans terres rares, combine fiabilité, performances et efficacité énergétique avec une classe de rendement IE5 » illustre Rodolphe Perault, chef de produits applications spécialisées dans le pompage. Il pointe l’empreinte carbone minimisée. « Cette solution a été développée conjointement avec les variateurs de vitesse et intègre des moyens de régulation adaptant la vitesse du moteur au débit nécessaire, à la pression voulue et au meilleur point d’efficacité BEP (Best Efficient Point) recherché de la pompe. » La gamme se décline en version compacte pour réduire le poids reposant sur la structure de la pompe, ou en version interchangeable avec moteur normalisé CEI pour la rénovation d’un équipement. De son côté, Danfoss Power Solutions vient de lancer son nouveau moteur à axe incliné à cylindrée fixe. « Ce moteur H1F représente l’évolution continue de la série H1. Bien qu’il s’agisse d’un nouveau moteur pour Danfoss, il tire parti d’une conception présente sur le marché depuis plus de 10 ans avec plus d’un million de kits rotatifs en service », explique Kenneth Befus, gestionnaire de la gamme hydrostatique. Léger et compact, le H1F est doté d’une enveloppe compacte à forte densité de puissance, avec sa faible longueur et son angle de 32 degrés. Conçu pour les applications en circuit ouvert et fermé, sur les machines agricoles, de construction et forestières, il offre un rendement global allant jusqu’à 95 %, et utilise le même groupe rotatif H1B à neuf pistons et une bride monobloc optimisée.
Sur les pas de l’électrification
La transition énergétique conduit à faire évoluer les moteurs, selon Rodolphe Perault : « nous réfléchissons à l’intégration au moteur de son électronique de pilotage sur la base du concept de l’ID300 (Varmeca auparavant) que nous proposons depuis plus de 30 ans. En effet, la configuration décentralisée autorise une plus grande flexibilité pour la conception de la machine et l’implantation des installations de production. » Ses avantages sont, entre autres, le gain de place, car elle ne nécessite pas d’armoire, la réduction des coûts d’installation et de câblage entre le variateur et le moteur ainsi que la diminution des pertes de puissance et l’émission des interférences. « Commander ID 300, notre solution de variateur intégré pour le pilotage des moteurs asynchrones IMfinity® de Nidec Leroy-Somer, comprend une application pompe intégrée avec régulation de la pression, pression constante / débit variable » complète le spécialiste. Cette fonctionnalité permet au système de gérer une pompe principale et de mettre en route jusqu’à trois pompes de soutien pour maintenir une pression constante si un débit élevé est nécessaire.
Mais l’électrification n’est pas possible partout. « Dans le domaine des machines mobiles à usage intensif telles que les broyeurs de pierres ou les déchiqueteuses, il n’est pas possible de convertir toutes les machines à moteur diesel, à fonctionnement mécanique et hydrostatique, en engins à entraînements alternatifs afin d’économiser du CO2. C’est pourquoi l’efficacité et le rendement de ces machines revêtent une importance croissante, pour réduire la consommation d’énergies fossiles » constate le Dr Peter Jaschke, directeur du développement commercial de Torsion Control Products (TCP) et de PT Tech (Allemagne). « Les accouplements à ressorts en acier de Torsion Control Products et les accouplements hydrauliques (Hydraulic Power Take-Off, HPTO) de PT Tech avec accouplement humide et un réducteur de distribution pour pompe ont fait leurs preuves. Les accouplements hydrauliques HPTO permettent d’activer ou de désactiver les machines de travail à transmission mécanique. Des raccords supplémentaires permettent de monter jusqu’à quatre pompes hydrostatiques afin de doter les machines de plusieurs circuits d’huile hydraulique » complète le dirigeant.
Dans les accouplements hydrauliques HPTO traditionnels, les sorties de pompe tournent toujours lorsque le moteur diesel est en marche. Or, certaines pompes tournent inutilement. « Avec le nouvel accouplement PTO lancé par PT Tech, ces pompes peuvent être désactivées afin d’augmenter le rendement de l’ensemble de la machine et de prévenir une usure accrue » précise Peter Jaschke.
Du nouveau dans la règlementation
Les normes européennes DIN EN 60034-30-1 : 2014-12 (fonctionnement sur secteur) et DIN VDE 0530-30-2 : 2019-02 (fonctionnement avec variateur de fréquence) définissent les quatre classes de rendement des moteurs électriques, E1 à IE4+. En fonction des mêmes critères de calcul, les entraînements encore plus performants sont connus dans l’industrie sous l’appellation IE5. Depuis le 1er juillet 2023, le rendement minimal des systèmes motorisés est modifié pour la mise sur le marché au niveau européen. Ainsi, le rendement IE4 est obligatoire pour les puissances comprises entre 75 kW et 200 kW des moteurs triphasés 2/4/6 pôles. Le rendement IE2 est obligatoire pour les moteurs à sécurité augmentée (Ex eb 2/4/6/8 pôles) dont la puissance est comprise en 0,12 kW et 1 000 kW. Il est aussi obligatoire pour les moteurs monophasés (2/4/6/8 pôles) d’une puissance comprise entre 0,12 kW et 1 000 kW.
Par ailleurs, le nouveau règlement machine a été transcrit en France en juin 2023. Il ne concerne pas directement les pompes hydrauliques, encore considérées comme des quasi-machines. « Le secteur de la transmission de puissance est concerné par l’aspect sécurité des commandes » résume Laurence Chérillat, déléguée générale d’ARTEMA.
Nécessaires économies d’énergie
Dans le coût total d’un moteur sur 10 ans, le prix n’entre que pour 2 %, la maintenance pour 3 % et l’énergie pour 95 %. « Notre énergie n’est peut-être pas encore assez chère pour déclencher des besoins. Agir sur les petits moteurs des machines tournantes en industrie comme en agriculture permettrait pourtant de répondre efficacement » constate Thierry Le Gal, directeur de Jet. « Mais l’obligation actuelle porte sur les moteurs d’une puissance supérieure à 75 kw alors que les économies pour notre environnement sont plus importantes pour les puissances inférieures » estime le dirigeant. Pour être le plus agile possible, il a mis en place des stocks en Bretagne de moteurs frein 2/4/6/8 pôles bi-vitesse, de IE3 et IE4 à partir de 75 KW et, surtout, un programme de fabrication d’IE4 à partir de 0,12 KW. L’entreprise intègre en effet Cantoni Motor (créé en 1878 en Pologne) qui produit des moteurs asynchrones triphasés à cages (de 0,09 KW à 5 000 KW) et Siti Riduttori (fondé en 1967 en Italie) avec ses réducteurs de vitesse notamment de couple conique qui, avec un rendement de 92 % répondent aux attentes écologiques. « Le remplacement d’un moteur IE2 Cantoni 0,37 kW par un moteur Cantoni IE4 a permis une économie de 41 €/an (10 h/j et 220 j/an 0,37 €/kW) pour un moteur de 172 €. Le remplacement d’un moteur IE2 Cantoni 30 kW-par un moteur Cantoni IE4 assure une économie de 668 €/an (10h/j, 220 j/an) pour un moteur de 3 200 € » chiffre Thierry Le Gal. Les économies portent sur toutes les applications. Ainsi, dans le cadre de la modernisation d’un parc moteur installé il y a plus de 20 ans, Nidec Leroy-Somer a conduit un projet d’optimisation énergétique portant sur 47 moteurs de 45 kW et 55 kW du bassin de traitement des eaux d’une station. La firme a proposé des motovariateurs synchrones à aimants Dyneo+ IE5, et chiffré les gains énergétiques et le temps de retour sur investissement avec son application Energy Savings Advisor, en intégrant les aides au financement prévues par le dispositif des Certificats d’Economie d’Energie. « Au final, l’unité a réalisé des gains énergétiques de 20 à 30 % et a diminué drastiquement son empreinte carbone, apportant ainsi une réponse concrète à la problématique environnementale » détaille Rodolphe Perault.
C’est aussi l’objectif de Nord Drivesytems avec son moteur synchrone à aimant permanent IE5+, moteur synchrone à 8 pôles à aimant permanent interne (IPM). Compact et économe en énergie, il offre un rendement élevé et constant de 93 % voire plus, sur une large plage de couples. « En d’autres termes, le moteur IE5+ permet d’économiser de l’énergie et, par rapport à un moteur asynchrone IE3 conventionnel, il réduit les émissions d’environ 0,15 t de CO2 par an » explique Frédéric Bénicy. Pour des projets plus ambitieux comme dans l’intralogistique par exemple, comportant des centaines voire des milliers de systèmes d’entraînements, l’économie totale réalisée est impressionnante. « Grâce à différentes innovations dans la conception du moteur, nous réalisons aussi d’importantes économies de matériaux », précise Jörg Niermann, responsable marketing de Nord. La taille des composants actifs du moteur est réduite, ce qui se traduit par des économies de minerai au niveau non seulement de la masse magnétique (empilement des tôles magnétiques), mais aussi de la quantité d’aimants nécessaires. Avec les moteurs synchrones à 8 pôles, le stator peut également être fabriqué avec des bobinages dits à denture unique. Par conséquent, les matériaux précieux comme le cuivre ne sont employés que là où ils sont réellement productifs, réduisant par là même une utilisation inefficace dans la tête de bobinage. Ces avantages s’appliquent non seulement au moteur IE5+ lui-même, mais aussi au motoréducteur DuoDrive, dans lequel l’IE5+ est intégré.
Mieux surveiller les défaillances
Ça bouge aussi du côté de l’instrumentation. « Nous pouvons voir comment la pompe ou tout autre composant industriel fonctionne réellement » illustre Chakib Mouhoubi, responsable vibration chez ifm electronic, qui lance en cette fin d’année 2023 une nouvelle gamme d’accéléromètres triaxes avec la technologie MEMS, des accéléromètres sans fil (WI-FI et Bluetooth Mesh), implémente ses algorithmes et propose un nouveau logiciel pour regarder les données historisées grâce à l’IA. Il poursuit : « nous récupérons toutes les données et nous les contextualisons pour fournir un réel bulletin de santé de la pompe afin de contribuer à la maintenance conditionnelle et prévisionnelle. Le monitoring peut s’effectuer 24h/24 grâce à la démocratisation de l’électronique, l’amélioration des performances des réseaux et des technologies plus accessibles financièrement. » La surveillance en continu repousse les limites des campagnes de mesures ponctuelles en identifiant des évènements transitoires, ainsi que l’évolution du comportement du composant en fonction de la production (dimensionnement, cavitation). « Notre boîtier ‘‘real time monitoring’’ peut lancer des alertes si les indicateurs retenus dépassent certains seuils. Il est également possible de créer un ‘‘modèle’’ de la pompe en ayant recours à l’IA pour chercher des indicateurs précoces de défaillance » ajoute Chakib Mouhoubi.
De son côté, KTR a développé un moyeu d’accouplement Rotex-GS sans jeu qui mesure le couple et la vitesse. En rotation, les données mesurées sont affichées sur l’accouplement, peuvent être envoyées via Bluetooth et consultées dans une application gratuite dédiée, Monitex. Dans le Monitex BT compact, l’ensemble de la technologie de mesure se trouve à l’intérieur du moyeu, ce qui permet d’intégrer facilement le couple-mètre dans des encombrements réduits pour la surveillance de machines, les bancs d’essai, le contrôle des process et l’assurance qualité, par exemple. L’informatique aide au choix et à l’installation des solutions. « Les moteurs, associés aux variateurs KEB, permettent une simplification de la mise en œuvre sur site grâce à une aide logicielle prévue pour les métiers du pompage. Les variateurs possèdent également un espace de programmation permettant de mettre en place des besoins spécifiques client » illustre Jean-Yves Geneste. La communication et l’intégration des fonctionnalités applicatives se généralisent. Par exemple, les moteurs d’igus sont utilisés entre autres dans le secteur de l’emballage, la technique d’inspection et le secteur alimentaire. Pour le pilotage d’entraînements linéaires et rotatifs, le réglage de la carte de pilotage peut se faire directement sur l’appareil ou, en tout confort, à l’aide d’un serveur web par l’intermédiaire d’un ordinateur portable, d’une tablette ou d’un smartphone.Chez Nidec Leroy-Somer, les fonctionnalités applicatives sont intégrées. « Les variateurs de la gamme Pump Drive F600 (1,1 kW à 2,8 MW), spécifiquement conçue pour le pompage, regroupent la prévention du fonctionnement à vide, le gavage du circuit, le nettoyage de la pompe, la protection contre les mises sous et hors tension, la régulation de niveau, la détection d’absence de débit. En complément, le variateur Powerdrive MD Smart est un modèle complet et prêt à l’emploi, 100 % connecté. Il intègre toutes les fonctions de protection, de contrôle et de raccordement nécessaires au pilotage d’un système de pompage jusqu’à 3 800 kW en toute sécurité. Avec ses fonctions logiques et sa capacité à s’auto-diagnostiquer, il offre des performances énergétiques optimales sur le contrôle des pompes, même à charge partielle » détaille Rodolphe Perault.
Configurez simplement vos ensembles moteur-réducteur
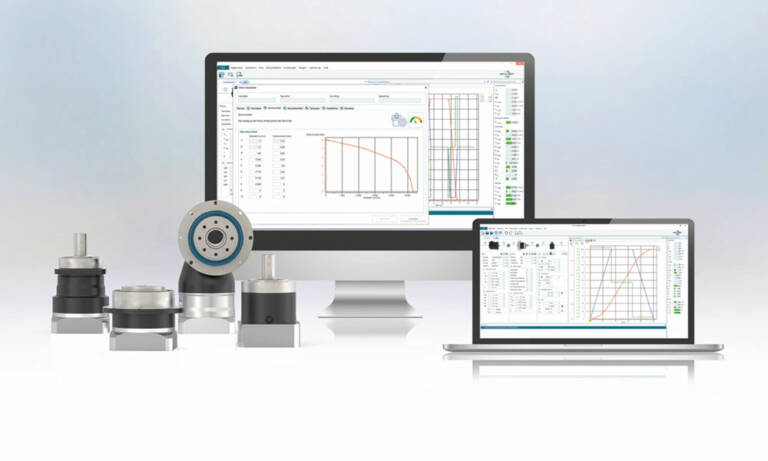
L’outil de configuration Neugart Calculation Program (NCP) détermine en toute fiabilité l’ensemble réducteur-moteur le plus rentable et offrant le meilleur rendement énergétique. Sa nouvelle version, NCP 4.3, améliore les performances du programme grâce à une utilisation optimisée du processeur multi-cœur. Mais avant tout, ce logiciel propose dès à présent de nombreuses fonctionnalités et optimisations supplémentaires, de la compensation aux entraînements à crémaillère.
Pour pouvoir configurer ou sélectionner la combinaison optimale de moteur et de réducteur propre à une application, les concepteurs peuvent calculer, dans le NCP, des courbes de charge complexes dans la chaîne cinématique. Fondé sur la pratique, le dimensionnement du moteur s’effectue sur la base de ses courbes caractéristiques avec visualisation graphique. Grâce à une base de données étendue, plus de 18 000 moteurs différents sont disponibles dans le NCP. La sélection ne se limite pas aux servomoteurs, mais compte également des moteurs pas à pas. De plus, la nouvelle version tient aussi compte de toutes les roues Neugart adaptées aux réducteurs NGV pour l’application d’entraînement. Au-delà de la base de données étendue, l’application elle-même a été étendue : ainsi, la compensation entre le dimensionnement théorique et les valeurs mesurées est encore plus facile.
Plus grande sécurité
Des menus déroulants réduisent au minimum les efforts liés à la préparation des données pour l’importation de la charge. Simultanément, la précision lors de l’importation de la charge de trace du moteur est encore plus élevée, car le calcul tient désormais aussi compte de l’inertie de masse du moteur et des pertes du réducteur. D’autres adaptations assurent une sécurité accrue lors du dimensionnement : en effet, les connaissances les plus récentes sont prises en compte lors de la mise en œuvre des bases de calcul actuelles. La sécurité statique des paliers est prise en compte dans les résultats des calculs. La vitesse d’avance des entraînements à crémaillère et pignon, quant à elle, est affichée sous forme de courbe graphique.
Confort accru pour les utilisateurs
De nouveaux détails apportés à la version NCP 4.3 offrent un confort accru lors de l’utilisation du programme : grâce à son ergonomie intuitive, même les utilisateurs novices ou occasionnels trouvent des exemples de dimensionnement pour chaque application avec une description détaillée. La gestion de projet est simplifiée du fait que l’application adaptée et les calculs déjà effectués peuvent être simplement consultés directement. Les fichiers peuvent être ouverts et les dimensionnements téléchargés facilement par glisser-déposer. Lors de la sélection du réducteur, l’utilisateur peut indiquer facilement les valeurs limites dans le filtre grâce à des champs de saisie supplémentaires. Des filtres sensiblement plus performants évitent les pauses durant la recherche du réducteur optimal. Grâce à une imbrication plus étroite avec le configurateur en ligne Tec Data Finder (TDF), on accède directement à la configuration produit correspondante.
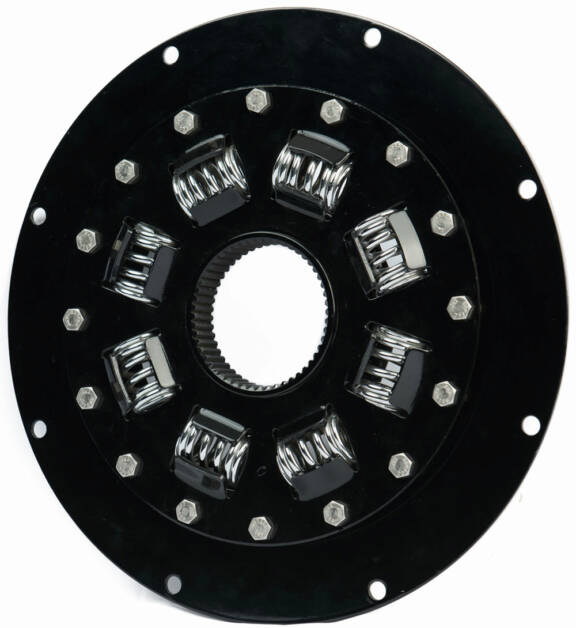
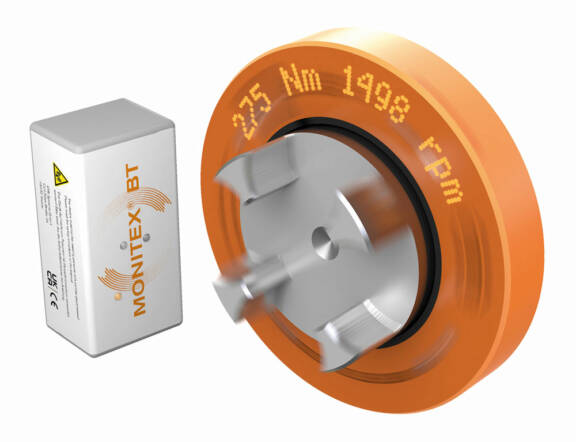
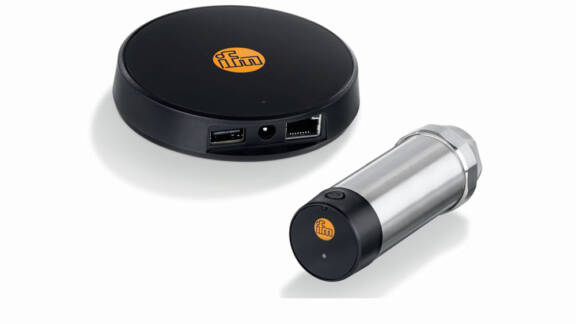
Vitesse variable et électronique intégrée
La voie est toute tracée, d’ores et déjà, pour la vitesse variable et l’intégration de l’électronique dans la mesure où les besoins en fonctionnalités s’étendent. « Les normes toujours plus contraignantes liées aux économies d’énergie justifient l’emploi de variateur en sus des progrès d’efficacité des moteurs et des pompes elles-mêmes » résume Rodolphe Perault. Patrice Baratte complète : « le futur sera aux solutions toujours plus intelligentes, innovantes et surtout communicantes ». Même écho chez Hydac : « Nous constatons une demande croissante de solutions d’entraînement électrohydrauliques complètes, accompagnées de logiciels électroniques et de modules matériels préinstallés qui peuvent être facilement et rapidement personnalisés » précise Nicolas Vieillard.
Demain, les informations récupérées seront encore plus nombreuses pour faciliter une maintenance préventive pertinente en récupérant les informations sur le courant moteur en permanence. « ifm electronic propose aux entreprises de déléguer leur maintenance préventive (en test aujourd’hui) avec leurs données placées sur le cloud et analysées par ses équipes : réception d’alerte par SMS ou mail pour gagner du temps de maintenance ainsi que de l’efficacité et soutenir les mainteneurs juniors ou ceux qui ne connaissent pas à fond les pompes » conclut Chakib Mouhoubi.
Un travail de normalisation très actif
Les normes connaissent des évolutions rapides liées pour beaucoup à l’électrification. Ainsi, l’aspect vibro-acoustique était peu normalisé jusqu’à présent, mais l’électrification réduit les bruits de moteurs et laisse donc émerger le bruit hydraulique. « Plusieurs thèses ont abouti et permettent à la France de bien avancer même si c’est très long car réduire le bruit des fluides s’avère complexe » souligne Alexandre Badev, expert hydraulique et pneumatique, responsable technique d’ARTEMA. Les méthodes de mesures sont en cours de normalisation et plusieurs textes se concrétiseront dans les prochains mois, sur la mesure et le traitement du signal acoustique ou le niveau d’onde de pression dans les transmissions hydraulique. Les experts espèrent, pour fin 2024, des normes sur l’efficacité énergétique dans l’hydraulique, en applications stationnaires et mobiles. Elle était jusqu’à présent déterminée à partir de l’arbre de la pompe. Début 2024 devraient par ailleurs être publiées trois nouvelles normes sur les performances des pompes et des moteurs : détermination de la cylindrée dérivée des pompes et des moteurs, détermination des caractéristiques des moteurs.
WEG, une étude de cas
La station de traitement des eaux Ashford Common est l’une des plus grandes d’Europe et fournit près d’un tiers de l’eau de Londres. Inaugurée en 1953, elle comprend 5 pompes à écoulement axial Weir Group, alimentées par des moteurs électriques de 7,5 t, chacune capable de pomper jusqu’à 180 000m3 par jour. En 2018, deux principaux problèmes affectaient les moteurs : la surchauffe, qui causait la dégradation de l’isolation et, malgré leur maintenance, les paliers qui arrivaient en fin de vie. L’isolation se dégradait au point de créer un court-circuit entre deux phases, imposant le rebobinage des moteurs. Certains avaient déjà été rebobinés trois ou quatre fois. Le constructeur de moteurs et de variateurs WEG a été retenu par les exploitants Thames Water, pour la robustesse de ses moteurs dans les environnements rudes et pour ses offres clé en main.
Il a travaillé avec BGEN (ex – Boulting group, spécialiste de la gestion de projets et de l’installation) pour moderniser les grands moteurs de pompes de cette installation. Ashford a choisi un moteur à bride haute performance WEG HGF de 600 kW, 415 V, à 10 pôles. La façon dont les énormes câbles électriques alimentent le moteur imposait aussi des idées novatrices pour gagner du temps d’installation. Neuf connecteurs se trouvent sur le côté alimentation et environ vingt-quatre sur le côté commande. WEG a donc fabriqué une boîte à bornes sur mesure pour conserver les mêmes presse-étoupes là où les câbles traversent le métal du boîtier de raccordement. Le premier moteur a été installé en 2019 suivi d’un deuxième, identique, en 2021. D’autres moteurs seront remplacés en 2024.
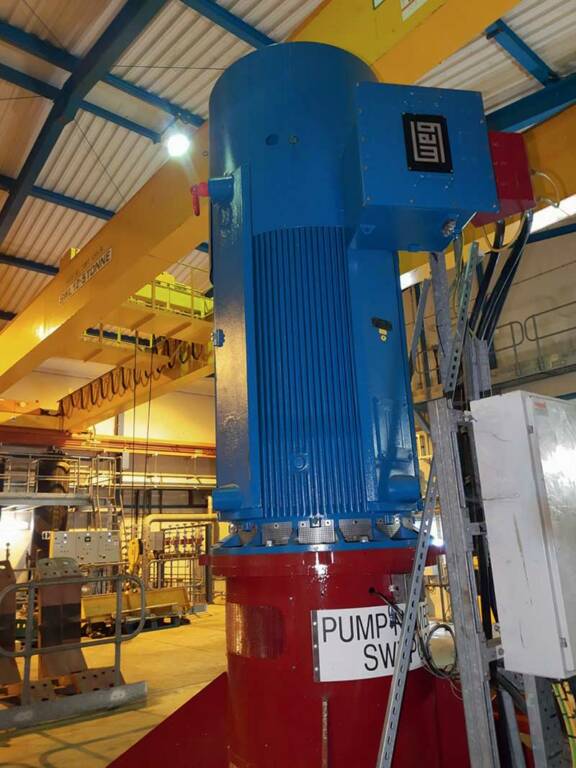