Filtration des huiles, air comprimé : des solutions orientées marché
De nombreuses défaillances hydrauliques sont la conséquence de fluides contaminés. Il en va parfois de même avec l’air comprimé, de plus en plus utilisé pour sa souplesse de mise en œuvre. Mais les contraintes imposées par les normes de qualité et le respect de l’environnement amènent les décideurs à considérer l’air comprimé comme une énergie à part entière. Pour l’huile comme pour l’air, les solutions sont nombreuses et constituent un investissement rentable.
Pascal Brion, responsable des ventes aftermarket filtration fuel-hydraulique chez Parker Hannifin, procède à quelques rappels généraux sur le maintien en propreté des fluides : « Il est de notoriété publique que 85 % des pannes sont liées à une huile polluée. En tant que spécialiste des systèmes hydrauliques, Parker met de plus en plus l’accent sur le fait que la technicité des composants, les coûts liés aux pannes et arrêts de machines sont autant d’arguments qui plaident en faveur d’une qualité d’huile viable sur le long terme. » Selon lui, le maintien en propreté se divise en deux catégories : en continu, grâce à la filtration qui retient la pollution particulaire. En parallèle, le flushing permet de nettoyer un fluide en profondeur. Le procédé permet la rétention des pollutions particulaires mais aussi liquides, notamment l’eau. Philippe Zorel, responsable commercial chez Hengst, rappelle pour sa part : « La filtration en particulier hydraulique répond à des règles précises et normées. En effet, séparer des particules solides d’un fluide hydraulique obéit au besoin de fonctionnement des appareils d’un système sensibles à la pollution. Tout système hydraulique s’use avec le temps que ce soient les composants d’une centrale par exemple ou le fluide lui-même (oxydation, hydrolise) et/ou ingère de la pollution extérieure (poussières d’atelier). Bien évidemment, tous les appareils sont conçus pour minimiser ces effets de la pollution mais nous ne pouvons ni les ignorer ni les éviter. »
L’eau, ennemi des composants hydrauliques
La présence d’eau dans l’huile hydraulique peut entraîner, en effet, la corrosion des composants. « Les industriels adoptent encore trop souvent une approche curative, déplore Pascal Brion. Ils traitent le problème dans l’urgence, avec des coûts et une perte de temps élevés. Parker Hannifin propose un concept baptisé gestion optimisée des fluides. En contrôlant un fluide, il est possible d’en déterminer le taux de pollution et d’agir en conséquence. »
En cas de non-pollution ou si celle-ci est faible, l’utilisateur est prévenu d’une action à mener à plus ou moins longue échéance. En cas de pollution, un traitement lui est proposé. « Le contrôle s’opère via un appareil baptisé iCount Particule Detector. » Ce module est installé à demeure. Il contient une technologie embarquée de pointe qui offre à l’ensemble des industries un détecteur de particules en ligne et une solution économique pour contrôler la contamination et la concentration en eau.
La solution prend la forme d’un unique appareil, le 10MFP-IPD, qui inclut le système de mesure. L’outil procède en trois temps : analyse, nettoyage, certification. L’iCount PD assure donc l’analyse et la certification, mais aussi le pilotage du process.
L’analyse en termes de particules et de teneur en eau obéit à la norme ISO 4406 :
Particules de 4 µ
Particules de 6 µ
Particules de 14 µ
% d’humidité relative : elle doit être inférieure à 100 ppm
De cette analyse, résulteront plusieurs actions telles que définir l’intérêt d’une dépollution (flushing) : savoir si le fluide peut être recyclé ou doit être changé ; détecter un problème lors d’une pollution anormale, et déclencher si nécessaire une analyse plus approfondie ; affiner la filtration, et par exemple changer le seuil de filtration à tel ou tel endroit ; valider les changements par une mesure finale.
« Les analyses avant et après traitement peuvent permettre de réorienter le choix de la filtration de protection, selon le type de polluants détectés, particules lourdes ou bactéries » complète Pascal Brion.
Le polishing est l’étape consistant à brasser le contenu d’un réservoir d’huile en aspirant et refoulant successivement son contenu, pour casser le dépôt sur les parois. Celui-ci peut être à l’origine de flexibles encombrés et de perte de charge. L’essentiel de l’eau et des bactéries sont ainsi évacuées.
Philippe Zorel détaille son approche dans le maintien en propreté des fluides : « au regard de la norme ISO 4406 (aka NAS 1638), les fabricants de filtres sont capables de définir leurs filtres destinés à maintenir ou à faire évoluer la classe de propreté du fluide afin que le système hydraulique soit en parfait état de fonctionnement. On peut lire par exemple, dans toute fiche technique d’une servo valve, que la classe de propreté nécessaire pour son bon fonctionnement est de classe 14/13/9 selon l’ISO 4406 (NAS classe 3). Alors le filtre du fabriquant de filtre doit être capable de fournir un filtre répondant à cette classe. »
Contraintes environnementales
David Schoendorff, responsable de département chez Hydac, signale que le maintien dans de bonnes conditions de service des huiles hydrauliques a considérablement évolué pour répondre aux exigences nouvelles des utilisateurs et aux contraintes environnementales imposées aux pétroliers : « La filtration particulaire traditionnelle évolue avec de nouveaux médias filtrants qui traitent d’autres aspects que les particules solides : problématiques de faible conductivité des fluides générant des décharges électro statiques et " brûlant " les huiles, phénomène limité par des éléments filtrants conducteurs agissant directement sur ces décharges. » « On rencontre de plus en plus fréquemment de problèmes de vieillissement d’huile générant des boues qui se déposent et bloquent les parties froides des systèmes, et sont traitées par des éléments en cellulose ayant une polarité similaire aux produits de vieillissement et donc s’attirent. L’introduction d’eau accidentelle est également plus fréquente en raison de la perte de la compétence en maintenance. Les solutions traditionnelles de déshydratation ne suffisent parfois plus et nous proposons des éléments coalescents séparateurs de phases en cas d’eau libre présente en forte proportion » ajoute David Schoendorff. Hydac a développé la gamme VEU de traitement par le froid des huiles afin de précipiter ces particules, puis de les capturer avec des éléments à base de cellulose. Pour des solutions plus compactes, le fabricant propose des groupes de traitement ayant un élément double couche de cellulose et fibre de verre, dont la caractéristique du cœur en cellulose permet d’attraper les produits de vieillissement sans ajouter une ligne de refroidissement. « Économiquement c’est la solution actuelle ayant le meilleur rendement Capex / Opex » souligne David Schoendorff.
Il illustre son propos de la manière suivante : « nos clients nous sollicitent souvent pour des huiles soumises aux dépôts de vernis évoqués qui bloquent des composants. Leur présence est mesurée par une valeur de colorimétrie dite MPC, dont la valeur critique est donnée à 30, pour une valeur " huile neuve " inférieure à 5, et bien souvent mesurée au-delà de 50. Dans ces cas de figure, nos groupes de traitement VEU permettent de gagner 10x classes de MPC en seulement 10 jours de traitement, et reviennent au bout d’un mois dans des valeurs sous MPC de 10, limitant ainsi tout arrêt pour changer des électro vannes bloquées, de la proportionnelle qui seraient devenues défectueuses. » Sur des machines neuves, comme des presses à injecter, « nous avons comparé deux centrales hydrauliques, une sans traitement et une avec traitement double couche de cellulose VEU5/3. Le résultat est sans appel : la presse avec notre groupe VEU 5/3 a vu son MPC stabilisé à seulement 4, soit une valeur d’huile neuve, ses classes de pollution particulaire ISO sont restées très stables à 15/13/10, et ce sur une durée de plus de 18 mois, sans aucune casse de composants. La presse sans groupe de traitement a vu sa pompe de circulation endommagée durant la période d’essais, ce qui aurait déjà largement rentabilisé l’achat d’un VEU 5/3. »
Les capteurs ont également évolué pour intégrer des fonctions de mesure de conductivité, de constante diélectrique, plus uniquement la perte de charge. L’utilisation d’algorithmes et de « machine learning » permet d’anticiper le colmatage d’élément filtrant en ayant une information de durée de service réelle restant à l’élément filtrant en service.
Filtration off line
ID System Fluid propose une gamme de produits de filtration qui complète le circuit de filtration en ligne et aide la filtration en ligne à dépolluer le lubrifiant pour atteindre des objectifs de propreté inférieurs aux niveaux de propreté cibles des composants. Ce système est appelé filtration hors ligne (Off-Line), où une pompe et un moteur dédiés font circuler et filtrent le fluide à partir du réservoir.
Le système est conçu pour tirer parti d’un principe de filtration appelé filtration radiale par micron. Ce principe est basé sur les éléments filtrants originaux uniques qui ont une finesse de filtration allant jusqu’à 0,5 micron et la capacité d’éliminer jusqu’aux plus petites particules de saleté. Les systèmes hors ligne peuvent être équipés d’une large gamme d’éléments en termes de taille de micron, de média filtrant et de compatibilité avec les fluides.
Pierre André, responsable de la mise en propreté des fluides chez ID System Fluid, souligne : « Les unités OLU (off line units) sont conçues pour rendre l’installation aussi simple que possible et pour maximiser l’encombrement de l’unité à proximité de l’équipement grâce à sa conception modulaire. ID System Fluid commercialise ces produits du distributeur Des-Case qui permettent, grâce à ces deux caractéristiques, de répondre aux besoins des machines en matière de propreté de l’huile et de surmonter les limitations d’espace et/ou de maximiser l’espace autour de l’équipement. »
Pierre André illustre son propos par l’exemple d’une grande entreprise d’extrusion d’aluminium en Autriche connaissant des pannes sur les joints spéciaux d’une presse à extrusion du groupe SMS. Cela a entraîné d’importants problèmes de contamination dans le système hydraulique de la presse. Les analyses de laboratoire ont déterminé des niveaux de propreté ISO de 24/22/18.
Vent d’efficacité dans les composites
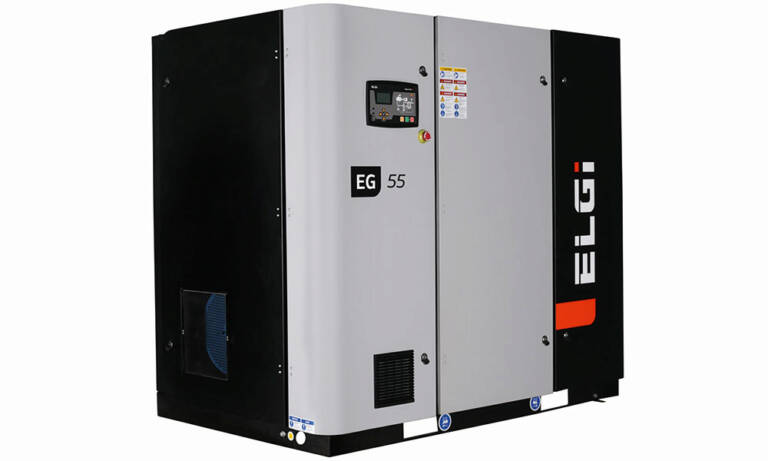
Le danois Dencam Composite a opté pour trois compresseurs ELGi de la série EG pour prendre en charge le fraisage de précision de composites, de bouchons, de moules et de modèles sur trois sites de production au Danemark.
Dencam Composite possède des années d’expérience dans la création et la production de solutions d’outillage composites dans les secteurs de l’énergie éolienne, marine et automobile. Lors de la sélection d’un partenaire d’air comprimé, leurs principales considérations étaient l’amélioration des processus de fabrication existants et l’identification d’une solution d’air comprimé fiable et économe en énergie pour alimenter leurs fraiseuses. Le spécialiste des composites a donc choisi trois compresseurs d’air à vis lubrifiés à vitesse variable de la série ELGi EG.
« Les coûts d’exploitation optimaux, l’efficacité énergétique et l’innovation sont les domaines prioritaires de notre entreprise. Des compresseurs d’air de haute qualité nous permettent d’y parvenir », estime Jens D. Andersen, PDG de Dencam Composite. « L’air comprimé économe en énergie est particulièrement vital, car nous produisons des moules utilisés pour créer les pales plutôt grandes des éoliennes. Nous sommes très conscients de l’importance de l’énergie alors que nous travaillons à la création de solutions d’énergie renouvelable pour l’avenir. »
La conception des compresseurs EG Series permet de fonctionner à des températures extrêmes, aussi bien froides que chaudes, et dans des conditions sèches à extrêmement humides, garantissant une plus grande fiabilité du système d’air comprimé. Ces compresseurs sont équipés de rotors à profil η-V développés en interne, avec la combinaison de lobes 4/5, conçus pour fonctionner à de faibles vitesses de rotation. Cette conception réduit les pertes de charge et, grâce au système OSBIC (séparation d’huile par impact et action centrifuge), la séparation en trois étapes offre le meilleur rendement énergétique de sa catégorie.
Pour résoudre le problème de contamination, le distributeur Des-Case a installé deux unités de filtration hors ligne RMF Systems (OLU4B, OLUS4B) avec un média de filtration en profondeur et un capteur de surveillance de la contamination (CMS). Ces unités de filtration agissent comme une boucle rénale dans le réservoir et éliminent les particules solides. Le CMS mesure et affiche automatiquement les niveaux de contamination de particules, d’humidité et de température dans le réservoir.
Résultat : le niveau de propreté ISO s’est considérablement amélioré, passant de 24/22/18 à 14/12/7. La durée de vie de l’huile a été prolongée de trois à cinq fois, ce qui a permis à l’entreprise d’économiser environ 1,5 million d’euros, et 23 000 € sont économisés à chaque fois qu’ils n’ont pas eu besoin de vidanger leur huile.
Distinguer maintien en propreté et dépollution
Philippe Zorel distingue le maintien en classe de propreté d’un fluide de la dépollution : « Le premier se fait sur un système qui a le plus souvent été " flushé " ou dépollué, pour le ramener à une classe conforme aux composants les plus sensibles du système. Ce maintien passe par l’utilisation de filtre capable de tenir en basse pression (environ 10 bars) jusqu’à la très haute pression (environ 450 bars). Ces filtres sont le plus souvent équipés d’indicateurs de colmatage optique et électrique mais aussi d’une valve bypass de sécurité en cas de surpression. »
Pour rappel, la dépollution d’un système est le passage d’une classe de propreté d’un fluide non conforme à son fonctionnement à une classe correspondant à son fonctionnement. La dépollution d’un système hydraulique se fait systématiquement à la mise en service du système et après des arrêts machine ou de changement d’huile, soit par rajout dans le réservoir soit par remplacement complet.
Philippe Zorel précise : « Cette dépollution est réalisée par des systèmes autonomes de filtration, indépendants de la centrale hydraulique appelé plus communément groupe de filtration. Ils sont dimensionnés en fonction du volume d’huile circulant dans la centrale hydraulique. Ces groupes de filtration peuvent être portatifs pour les plus petits ou sur chariot roulant pour les plus gros. Ils sont tous équipés à minima d’un groupe motopompe et d’un filtre. Ils doivent disposer de la certification CE machine puisque ce sont quasiment des machines. »
D’autres appareils sont utilisés, notamment pour la désaération et déshydratation de l’huile, appelés purificateurs. « L’eau sous forme d’humidité (eau dissoute et eau libre) et l’air sont des ennemis du bon fonctionnement des appareils. Outre la corrosion, l’eau conduit à la perte de performance des huiles par réactions chimiques (oxydation, hydrolyse). Enfin, les capteurs permettent de contrôler le niveau de propreté de l’huile ainsi que sa teneur en eau (libre), tels que des compteurs de particules. Ils se positionnent directement sur la centrale hydraulique et réalisent des mesures en temps réel. »
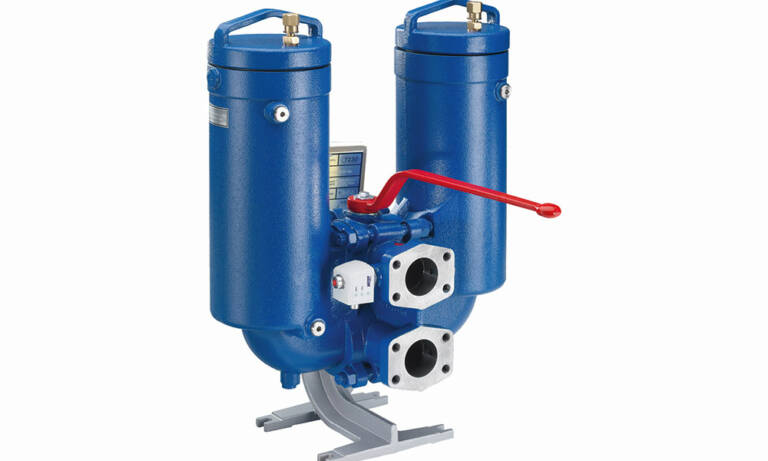
Les cinq commandements
Selon Philippe Zorel, la bonne filtration répond à cinq facteurs : l’assurance du filtre d’atteindre la classe de propreté définit par les composants ET DE LA MAINTENIR le plus longtemps possible. La Delta P du filtre, autrement dit la perte de charge initiale et finale que génère le filtre lors du fonctionnement de la centrale. L’efficacité de filtration (%) ou le coefficient bêta qui définit le nombre de particules retenu par l’élément filtrant (ou cartouche) dans des conditions précises définies aussi par des normes.
Du nouveau chez MP Filtri
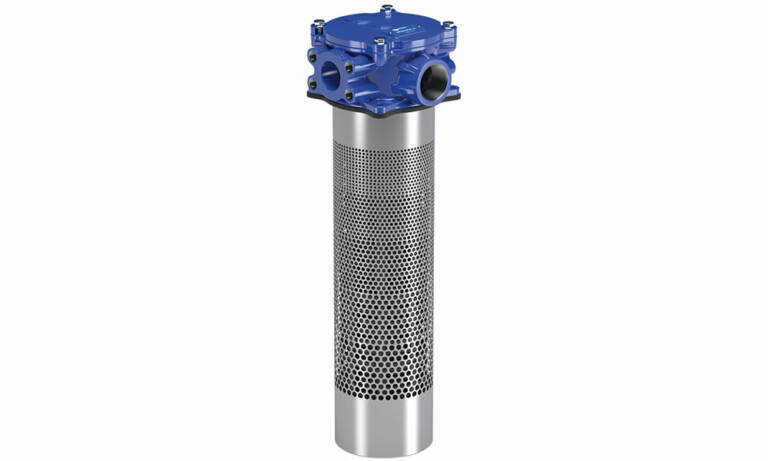
Le fabricant a commercialisé, en novembre 2023, un filtre de retour de dégazage permettant de réduire le flux d’air dans le réservoir. Il affiche une pression de service jusqu’à 10 bars (145 psi), des débits jusqu’à 500 l/min (132 gpm), des raccords filetés 1 ", 1 1/4 " et 1 1/2 " GAS/NPT/SAE " et des raccords à brides 1 1/4 " et 1 1/2 " SAE 3000.
Le filtre de désaération « sans bulles » MDH 250 permet de réduire le flux d’air dans le réservoir à travers le filtre. Grâce à ses multiples connexions et à son indicateur différentiel, il s’adapte à tous les systèmes. Le filtre est composé d’éléments clés, notamment une membrane anti-drain, une vanne de dérivation, un élément filtrant avec une conception innovante de la trajectoire d’écoulement et un diffuseur intégré au filtre.
À la même date, MP Filtri a lancé le CML4, son nouveau moniteur de contamination portable et compact, un laboratoire mobile qui excelle sur le terrain. Léger et durable (8,5 kg), il est doté d’une cellule de protection interne en acier à fort impact et peut fonctionner toute la journée avec une seule charge de batterie. Doté d’une technologie optique et photodiode innovante permettant une mesure complète sur 8 canaux, le CML4 fournit une évaluation rapide et précise de la contamination par les particules et l’eau dans les fluides hydrauliques, les huiles synthétiques et le diesel.
Le coefficient alpha s’exprimant en grammes qui définit aussi la quantité massique qu’un élément filtrant peut retenir à une delta P déterminée normalisée aussi. La valeur économique du filtre. « Pour obtenir la satisfaction client, nous proposons des produits qui permettent le meilleur fonctionnement de la machine en étant efficaces et discrets c’est-à-dire que le client trouve une grande simplicité à les utiliser sans être en alerte systématiquement. Pour cela, il n’y a pas que le produit qui compte mais tous les services connexes de notre entreprise : le commercial, l’administration des ventes, la logistique, la technique » estime-t-il. Hengst vient de commercialiser une nouvelle gamme de filtres moyenne pression (250 bars), la série 250 LEN. Cette gamme est axée sur la simplicité de maintenance. Bien dimensionnés, ces filtres sont efficaces. Les éléments filtrants à l’intérieur des corps de filtre ont une durée de vie très performante grâce à leur média Pure Power. Ils sont simples à changer après colmatage, ce qui évite les pertes d’huiles et permet une purge rapide.
Quelle qualité de l’air ?
Festo intervient principalement sur la qualité de l’air. Les utilisateurs de machine fonctionnant avec de l’air comprimé ont besoin d’un air d’une qualité suffisante pour éviter d’endommager les composants pneumatiques. Le fabricant entend, pour ce faire, éliminer trois types de contaminants : les poussières, particules solides, l’eau et l’huile. L’huile et les poussières peuvent s’accumuler et finir par boucher certains orifices, comme dans les distributeurs, rendus inutilisables. La présence d’eau peut avoir plusieurs effets négatifs : la corrosion des pièces en acier, en particulier. À basse température, l’eau se solidifie en glace, qui peut bloquer les pistons des vérins.
Ça a été le cas d’un client qui utilisait des vérins pneumatiques en chambre froide, en dessous de – 30 °C : « Après plusieurs casses de vérins, nous sommes parvenus à la conclusion que l’air comprimé contenait trop d’humidité, qui se transformait en glace lorsque l’air comprimé stagnait dans les vérins. La glace finissait par détruire les joints et casser les vérins. Dans ce cas, nous avons proposé un assécheur à membrane pour abaisser le point de rosée au-delà de la pression ambiante. Depuis cette modification du circuit de conditionnement d’air comprimé, plus aucune casse n’est à déplorer. »
Parmi les solutions proposées, Festo évoque la série MS, une gamme complète de fonctions pour la filtration. Des filtres à particules de différentes tailles, de 40 µm au centième de microns. Pour la suppression de l’huile, la solution avancée par le fabricant est la filtration à charbon actif. Pour la suppression de l’eau, plusieurs types d’assécheurs existent : les séparateurs d’eau, qui sépare l’eau à l’état liquide de l’air comprimé. Les sécheurs à membrane, qui permettent d’abaisser le point de rosée de 17 °C et les sécheurs à adsorption qui abaissent le point de rosée de 50 °C. Tous ces filtres peuvent être combinés avec les autres composants nécessaires au conditionnement de l’air comprimé : les vannes de coupure manuelle et électrique, les régulateurs de pression, les vannes de mise en pression progressive.
Le fabricant indique : « Nous proposons en parallèle aux utilisateurs de machines, des services d’audits de la qualité de l’air pour s’assurer du bon fonctionnement des équipements de génération et de filtration de l’air comprimé. »
Des exigences différentes
Afin de vérifier la qualité d’air comprimé utilisé pour le process, Beko Technologies a réalisé une mesure mobile sur le réseau pour le compte d’un industriel du secteur pharmaceutique. Ce dernier possède plusieurs bâtiments de production et unités de fabrication. Tous utilisent l’air comprimé, principalement comme air de régulation, mais ont tous des exigences de qualité différentes, en fonction de son contact direct ou indirect avec les produits.
L’analyse a permis de déterminer l’état réel de l’air comprimé au niveau de l’entrée de chaque bâtiment décentralisé, qui ne correspondait pas aux exigences de qualité fixées par le service qualité, d’où la nécessité d’améliorer le système de traitement d’air comprimé existant.
L’industriel disposait déjà d’une centrale de production d’air comprimé exempte d’huile associée à des sécheurs Everdry de Beko, installés en aval. La difficulté était que les unités de fabrication sont alimentées depuis une production d’air comprimé centralisée située à plusieurs centaines de mètres.
Pour y remédier, le fabricant a préconisé d’associer le système existant à une solution de traitement décentralisée à l’entrée de chaque bâtiment. Cette solution est composée d’adsorbeurs à charbon actif avec une ligne de filtration comportant un préfiltre, deux filtres antipoussières oil free, un filtre micronique et un filtre à charbon actif oil free (sans huile) couplé à une option bypass. Le séchage centralisé de l’air comprimé ayant rendu obsolète un séchage supplémentaire, l’accent a été mis sur la ligne de filtration.
Afin d’avoir une maîtrise parfaite de la qualité de l’air comprimé utilisé pour ses processus selon la norme ISO8573-1, l’industriel a, en outre, opté pour l’analyseur de la teneur en huile résiduelle de l’air comprimé METPOINT OCV compact, un compteur de particules PC 400, un dispositif d’analyse du PRSP et un enregistreur des données air comprimé avec 4 entrées de capteur.
Le dispositif technique composé d’un adsorbeur à charbon actif, associé à une ligne de filtration (préfiltration et filtration aval) correspondantes, constitue une solution de traitement adapté dans ce secteur d’activité.
La démarche de Parker en matière d’air comprimé consiste à identifier les polluants à éliminer ou dont la teneur doit être drastiquement abaissée. David Chabredier, digital account manager, précise : « Cette notion de polluant est totalement différente d’une industrie à l’autre, et les polluants identifiés pour actionner des vannes dans une carrière ne sont pas les mêmes que ceux à éliminer pour un contact direct avec du lait infantile ou une puce électronique. L’air comprimé c’est mille et un besoins différents. Pour répondre à tous les cas de figure, Parker dispose d’un arsenal complet de technologies destinées à purifier l’air comprimé quel que soit la qualité finale attendue et surtout quelle que soit la technologie de compresseur utilisé (lubrifié ou non) : filtration, sécheurs d’air, colonnes charbon actif, catalyse CO/CO2, équipements dont les caractéristiques sont adaptées à chaque besoin spécifique. »
Pour exemple, il cite la gamme de filtration Oil X Parker. Celle-ci se décline en 4 grades dont l’efficacité a été testée, validée et certifiée par un organisme externe et indépendant, la Lloyds Register. Le grade WSP : séparation des liquides avec efficacité certifiée selon l’ISO 8573-9 et l’ISO12500-4s, le grade AO, filtration déshuilante coalescente et/ou particules sèches 1µ certifiée selon l’ISO 8573-2 et – 4 ainsi que selon l’ISO12500-1, le grade AA, filtration déshuilante coalescente et/ou particules sèches 0,01µ certifiée selon l’ISO 8573-2 et – 4 ainsi que selon l’ISO12500-1 et le grade ACS, charbon actif pour rétention des vapeurs d’huile, goûts et odeurs certifiée selon l’ISO8573-5 et l’ISO12500-1. Parker développe également des solutions spécifiques innovantes telles que les unités de traitement d’air OFAS (Oil Free Air System) garantissant un air comprimé propre et sec tout en affichant une classe 0 en huile, et ce même en cas d’installation en aval de compresseurs lubrifiés. Cette classe 0 en huile est certifiée par la Lloyds. « Cette nouveauté dont l’efficacité est mesurée et prouvée a pour but de protéger et garantir de manière efficace et économique les moyens de production et les produits finis contre toute éventuelle pollution, tout en évitant d’investir dans des technologies de compression exemptes d’huile (dites oil free) réputées coûteuses en investissement et maintenance » estime David Chabredier.
Oilgear a développé la gamme Air Dry Filter pour la purification de l’air entrant et sortant des réservoirs de grosse capacité. Cette solution technologique de filtration et assèchement de l’air combine trois avantages : la maîtrise du niveau de pollution particulaire de l’air atmosphérique qui entre dans les réservoirs avec transfert de volume important, la suppression de brouillard d’huile rejeté dans les ateliers de fabrication, l’élimination des contraintes mécaniques des parois de réservoir lors des transferts de volume d’huile. Patrice Baratte, responsable des ventes en France, souligne que « pendant les mouvements de la presse, de gros volumes d’huile sont déplacés dans le réservoir. Lorsque les filtres à air standards sont saturés par l’air chargé de gouttelettes d’huile, la delta P augmente aux bornes des éléments filtrants standards et cela provoque des pressions et des dépressions à l’intérieur des réservoirs (" mauvais effet de respiration "). »
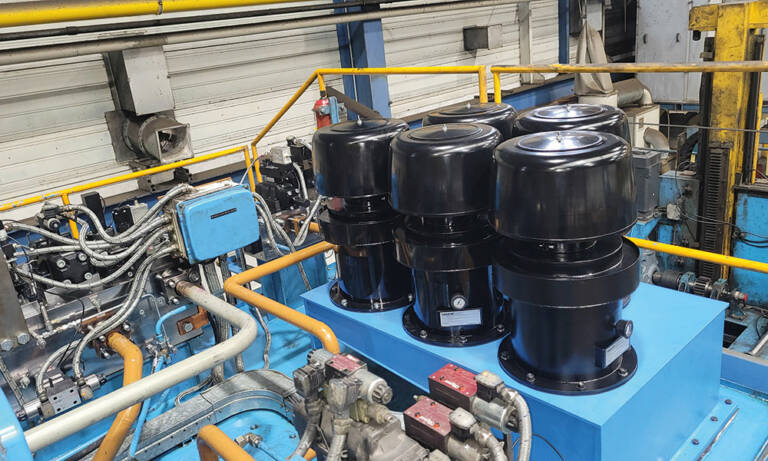
Total ANAC, l’expertise fluides hydrauliques
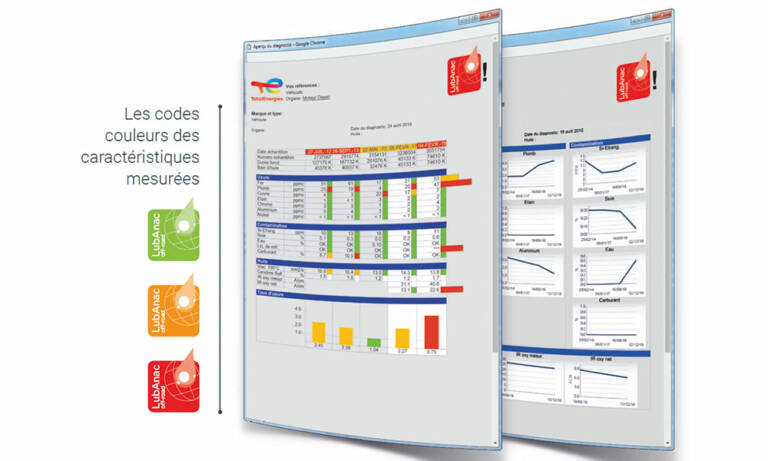
L’analyse de fluides hydrauliques par le laboratoire Total ANAC (analyse de lubrifiants) contrôle l’ensemble des critères permettant d’effectuer un bilan de santé de l’huile en service : paramètres physico-chimiques, métaux d’usure, présence des additifs et polluants extérieurs.
Total ANAC a donc compilé des milliers de diagnostics sur les organes hydrauliques/hydrostatiques. Il en ressort les deux constats suivants : à l’échéance des intervalles de vidange, 90 % des bilans sont vert et ne démontrent aucune déviation négative des différents critères mesurés ; d’autre part, la principale cause de dysfonctionnement est la pollution : silicium, eau.
Stéphane Millot, ITC Grands Comptes Lubrifiants, souligne : « Le suivi analytique permet donc d’éviter la vidange systématique et l’analyse garantira que le fluide peut continuer son service en toute sécurité technique. En cas de pollution, Total ANAC propose à ses clients différentes solutions de filtration afin de libérer l’huile de tous éléments étrangers. »
Le service propose des solutions complètes de dépollution : groupe de filtration, filtre, compteur de particules ou étude. Après application des différentes étapes de maintenance, cela permet une économie d’un changement de fluide du circuit hydraulique. Les premiers clients grands comptes qui ont suivi cette démarche totalisent aujourd’hui des bains d’huiles hydrauliques à plus de 6 000 h de fonctionnement.
En conclusion
Festo se projette dans le cadre de l’industrie 4.0. Dans une usine connectée, la fonction de conditionnement de l’air doit elle aussi être connectée. « Nous intégrons donc de plus en plus d’appareils directement dans la ligne de traitement d’air pour commander l’ouverture et la fermeture de la vanne d’alimentation, des capteurs de pression et de débit pour suivre la consommation des lignes de production, ainsi que des capteurs de colmatage des filtres pour planifier au mieux les opérations de maintenance » indique Festo.
Pour Philippe Zorel, « l’avenir de l’hydraulique montre que nous allons vers des pressions de plus en plus élevées et des fluides de plus en plus performants et exigeants. Le faible encombrement est aussi un facteur. Le mètre carré coûte de plus en plus cher. Nous ne sommes plus à l’heure de construire des systèmes très encombrants, gros consommateurs d’énergie, mais plutôt vers des centrales hydrauliques plus compactes avec des volumes d’huile moins importants et des pressions de fonctionnement plus élevées, parfois même assisté de source d’énergie électrique. Nous sommes à l’ère de l’utilisation de fluides de moins en moins polluants. Le passage à des huiles de moins en moins minérales tels que des esters ou des fluides ne contenant plus de zinc ou de nickel se développent. Cela nécessite de s’adapter et de donner une réponse technologique performante et économique à ces évolutions. Le niveau élevé de propreté des systèmes hydrauliques attendu sera nécessaire pour garantir la fiabilité des systèmes hydrauliques et des systèmes d’huile de lubrification. »
Chez Parker, David Chabredier considère que « l’avenir est aux solutions orientées applications et marchés, telles que nos nouvelles unités FBP (Food – Beverage – Pharma). Ces unités de traitement d’air tout-en-un ont été désignée pour répondre aux besoins de qualité d’air pour les applications les plus sensibles touchant aux secteurs de la " life science " (agro-alimentaire, pharmaceutique cosmétique), en intégrant toute la certification nécessaire pour les audits : qualité d’air certifiée selon ISO par la Lloyds Register et certification FDA pour les matériaux, en plus de la certification des performances du sécheur, sans négliger les performances énergétiques grâce au mode ECO de série. »
David Schoendorff, d’Hydac, considère que « certains fluides vont disparaître au profit de nouvelles technologies en croissance, comme dans le cas des véhicules électriques. La production de ces derniers nécessite trois à quatre fois moins de pièces mécaniques, donc d’usinage et de fluides de coupe. Les autres fluides devront tenir des durées de service bien plus longues et les solutions de traitement devront donc s’adapter afin de minimiser les appoints. Leur recyclage sera non seulement étudié d’un point de vue prolongation de leur durée de vie, mais nos solutions devront également mettre en avant leur capacité à récupérer les calories dissipées dans le fluide pour réinjecter cette énergie perdue dans d’autres process comme le chauffage de bâtiments. Ce sont ces solutions qui seront efficientes : non seulement un fluide " durable " mais multi-usage et facilement recyclable en fin de vie. »
Pierre André, d’ID System Fluid, conclut : « À l’avenir, nous continuerons à optimiser les performances des filtres afin de maximiser leurs capacités à résoudre les problèmes complexes liés aux polluants de l’huile pour différents types et viscosités de lubrifiants, mais aussi à soutenir les objectifs économiques et environnementaux des clients et des marchés. »